Large aperture and high-precision aspheric mirrors are core components of optical telescopes, and their manufacturing processes require the use of multiple advanced optical processing technologies. Among these, robotic CNC polishing technology is one of the most widely used techniques.
However, due to the significant edge effects caused by the polishing tool at the mirror's edge, traditional CNC polishing methods often require replacing the tool with a smaller one to specifically correct the mirror's edge errors. This substantially impacts the efficiency of mirror manufacturing.
Therefore, how to suppress edge errors without changing the tool during a single processing cycle and achieve full-aperture convergence, encompassing both the central and edge areas, presents an important pathway for enhancing mirror manufacturing capabilities.
Following extensive research and practical application, the Research Lab for Astronomical and Space Mirror Technology at Nanjing Institute of Astronomical Optics & Technology (NIAOT) of the Chinese Academy of Sciences has made significant progress in full-aperture CNC polishing technology.
Recent advancements by our research group have introduced an innovative numerical control (NC) grinding and polishing method with a variable orbital radius, enabling efficient full-aperture figure convergence for mirrors. This technique employs two distinct dwell time models for material removal functions: spatially invariant models in the central region to minimize computational load, and spatially variant models in the edge region to enhance precision in figure control.
Following the calculation of dwell times for both the central and edge regions, a fused polishing trajectory utilizing the variable orbital radius technique integrates the results, generating a robotic control program (as shown in Figure 1). This method achieves full-aperture figure correction of the mirror within a single processing cycle without requiring tool changes, and it demands minimal hardware, facilitating its application across various mirror types and the development of batch processing systems.
This method, titled "Efficient full-aperture mirror polishing method with variable orbital radius in computer-controlled optical surfacing," was published in the internationally renowned optics journal Optics Express, Volume 32, Issue 13 (paper link: https://doi.org/10.1364/OE.523657).
The first author of the paper is doctoral student Zhou Jianjie, supervised by Professor Li Xinnan and Li Bo from NIAOT, with Professor Li Bo serving as the corresponding author. This research was supported by the National Key R&D Program (2023YFA1605602), the National Natural Science Foundation of China Major Instrumentation Project (11627804), and the General Project (11873070).
NIAOT actively applied this technology to several advanced telescope mirror manufacturing tasks, where it played a critical role. These include the single-mirror primary mirror of the 2.5-meter large-field high-resolution solar telescope (as shown in Figure 2) and the 18 segmented mirror pieces of the primary mirror of the 4.4-meter spectroscopic telescope (as shown in Figure 3).
Both of these telescopes are among the most advanced optical telescopes in China's current astronomical field. Based on its self-developed mirror manufacturing technology and focusing on its core responsibilities, the research institute continues to exert efforts in the development of advanced astronomical telescopes and breakthroughs in key technological innovations.
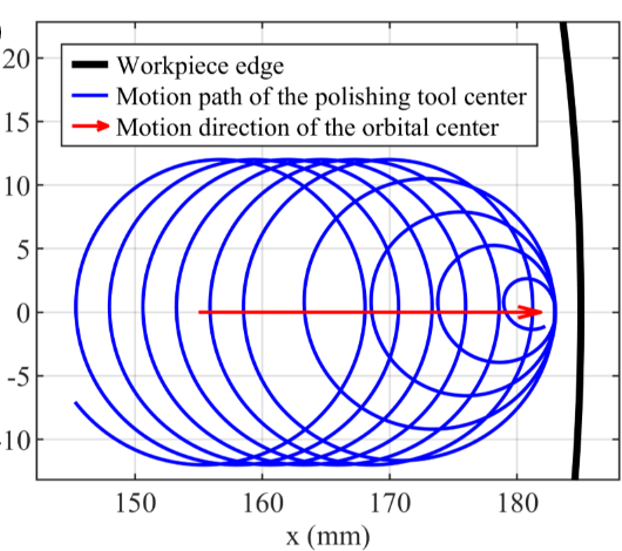
Figure 1: movement path of the center of the polishing tool under changing orbital radius
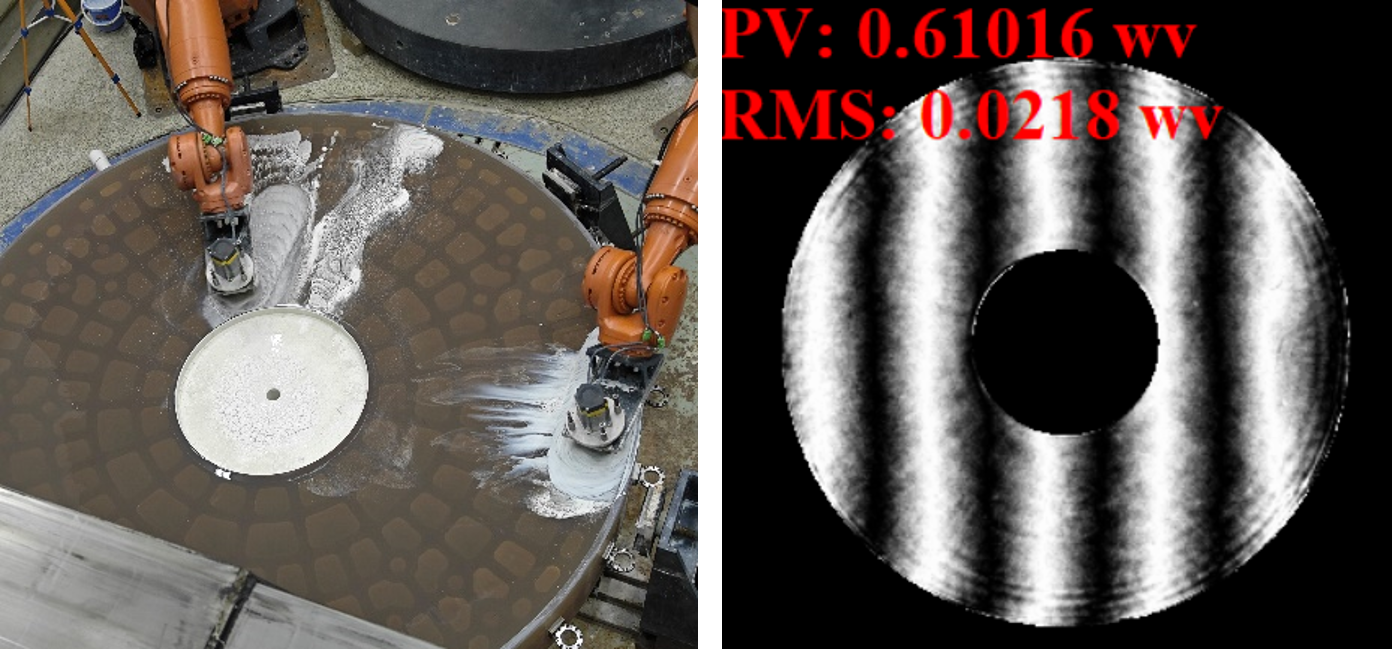
Figure 2: Application of new technology to the primary mirror processing of the 2.5-meter large field-of-view, high-resolution solar telescope: (left) CNC polishing with collaborative robots (two robots working together); (right) interferometric fringe pattern of the completed surface of the primary mirror
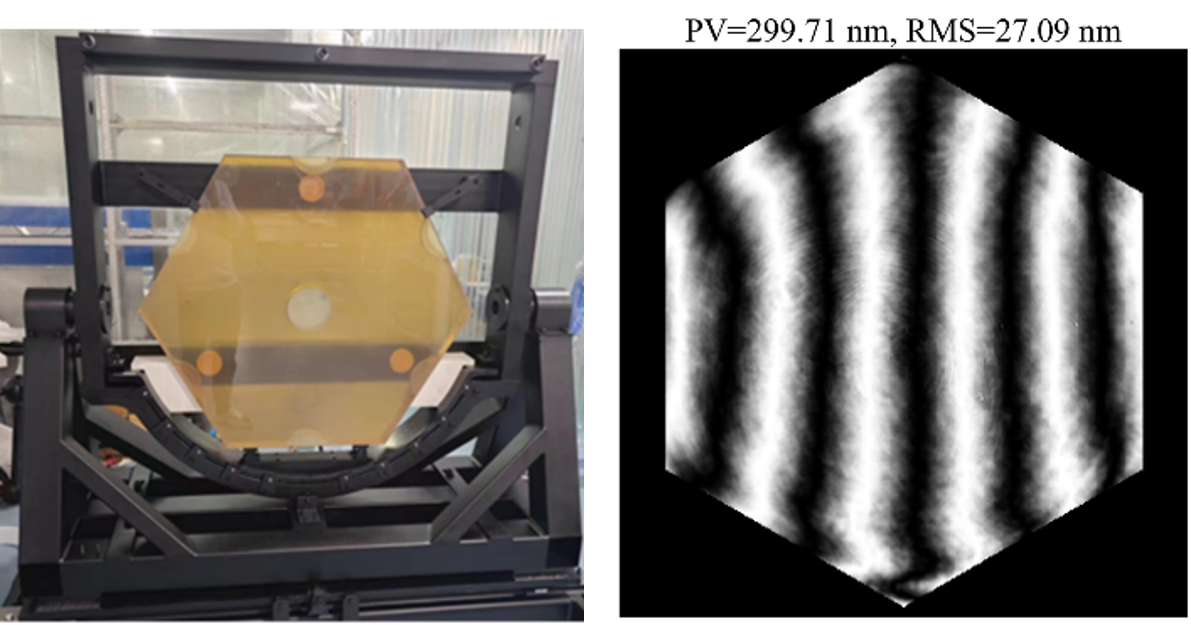
Figure 3: Application of new technology in the production of the 4.4-meter spectroscope telescope's mirror segments: (Left) hexagonal mirror segments after cutting; (Right) interference fringe pattern of the mirror segment surface shape after completion of robotic CNC polishing
DOI: https://doi.org/10.1364/OE.523657